業務効率向上だけじゃない工場の省人化とは
~ 品質向上・人手不足解消にもつなげる省人化のメリットと成功事例 ~
公開日:2022/02/02 更新日:2024/12/23
リモートコントロール

AIやIoTといった新しい技術を活用し、無駄な工程を削減することで業務効率を上げる取り組みが多様な業種で進められています。物流にITを活かした「物流テック」、遠隔制御による施設管理などを始めとした小売業で盛んに進められているイメージがありますが、医療や介護施設でロボットを活用するなど、省人化は多様なシーンで活用されています。工場の省人化もそのひとつで、少ない人数で効率よく生産ラインを行うことで、人員コストの削減だけでなく、品質向上においても有効とされています。
この記事では、工場の省人化に焦点を当て、業務効率向上以外に期待できるメリットとその方法、また食品工場および大手メーカーの事例をご紹介します。
1. 工場の省人化は工数の削減が主な目的
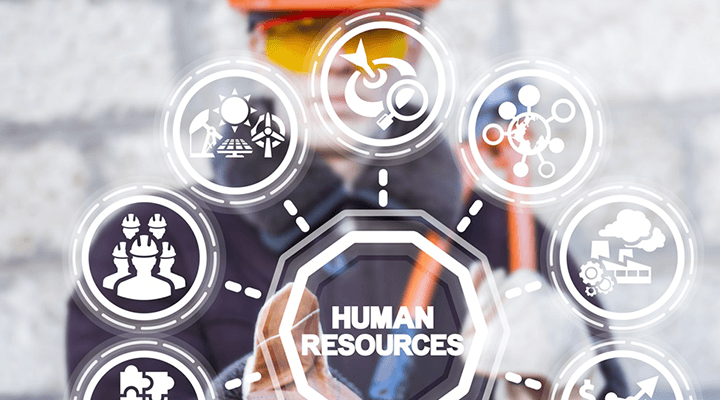
省人化とは、工場設備や作業工程の見直しを行い、改善策を考え、人員を削減することを意味します。似たような用語に、省力化と少人化というものがあり混同されがちですが、それぞれ少しずつ意味が異なります
- 省人化と省力化の違い
- 省人化と少人化の違い
いずれも、作業の内容や方法を見直して無駄をなくし、工数を削減することを目的とした用語です。ただし、結果としてなにを目指すのか、目的に違いがあります。
省人化と省力化の違い
省人化は、トヨタ生産方式で使われるようになった用語で、工場においては作業者の人数を削減することを目的とした取り組みを指します。省力化は省人化の前提ともなる部分で、無駄を省き作業効率を上げることを目的とした取り組みを意味します。
作業内容をチェックしたのち、少ない工数でこれまで通りの成果を出すことで省力化したり、ロボットなどを用いて自動化したりなど、大きく省力化できれば、人員数削減につながるため、それは省人化に成功したということになります。
省人化と少人化の違い
少人化も、トヨタ生産方式で使われるようになった用語です。少人化は、需要の変動にあわせて作業者の人数を変動させること、つまり常に最適な最少人数での生産ラインの運営や、その取り組みを意味しています。そのためには、作業内容が誰にでもできるようマニュアル化されている必要があります。
しかし、各作業員が受け持つ設備や工程が決まった運用をしている、いわゆる属人化に該当される形態を採っていると、その設備を使った作業しかできず、他の作業員も設備を使った作業に従事することができません。
こういったケースで少人化を目指すのであれば、ラインごとの生産品目を増やすライン統合や、作業者が複数ラインを掛け持ちできるような工夫をするなどの対処が必要になってきます。
2. 省人化の3つのメリットと2つのデメリット
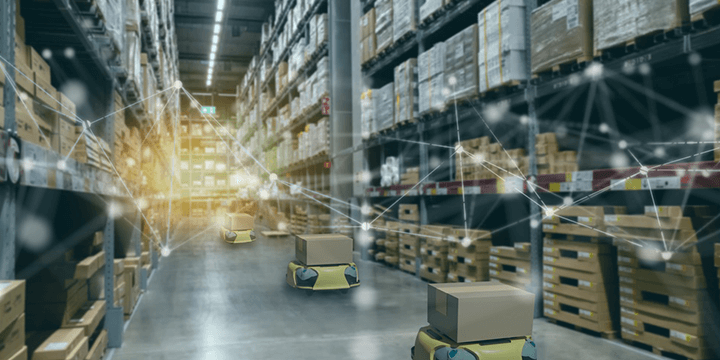
省人化には人員コストの削減や、労働人口減少に適応可能などさまざまなメリットがありますが、そのための資金が必要不可欠となります。また、現代におけるロボットや設備の管理や監視には、システムの導入が欠かせません。それに伴う省人化のメリットとデメリットについて、詳しく見ていきましょう。
省人化の3つのメリット
省人化を進めるにあたって、これまでの作業工程を洗い出し、自動化や標準化を図ります。その結果、一人ひとりの作業員の作業効率を上げるだけでなく、均一化された品質をキープでき、トラブル発生を想定したマニュアル化された対応ができるなどさまざまなメリットが挙げられます。
- 従業員ひとりひとりの負担を軽減し、人材不足の解消にもつながる
- 生産や検査の自動化により一定水準の品質を保持できるようになる
- ベテラン作業員のスキルに依存せず、誰でも同じ精度で作業を遂行できる
とくに高齢化が進み、人材の確保が厳しくなっていくこれからの時代においては、省人化を進めていくことはリスクマネジメントの視点からも有効といえるでしょう。
なお、就業者の高齢化に加え、省人化が進んでいないことを原因に、従業員の業務中の死傷事故につながることも危惧されています。人材不足の解消のみならず、人材の安全を担保するためにも今後ますます省人化は注目されていくでしょう。
省人化のデメリットである2つのコスト
省人化を実現するためには、AIやロボットを使った自動化を手法とするケースが多く、システムや設備を導入するための投資コストが必要になります。
また、システムの運用や管理をするには、相応の専門的スキルを持った新たな人員が必要となることもあります。設備と人員といった2つのコストを投資したものの、アウトプットとしての業務効率につながらず、結果としてコスト削減はおろか余計なコストがかかってしまう結果となる事態も発生しがちです。加えて、現場担当者へのヒアリングを十分にしないままシステム構築をしてしまったことにより、実情にあわず現場での負担が減らないといった懸念事項もありますので、十分な事前準備が必要となるでしょう。
業務効率の向上に加え、品質の向上や人手不足を解消することを目的とした省人化のメリットを最大化させるには、事前準備が重要になります。次の項目では、省人化を行う方法を見ながら、自社にとって何が必要かを考えていきましょう。
3. 省人化を行う方法
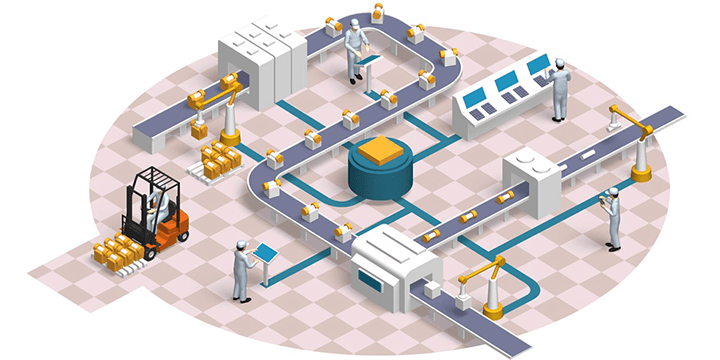
省人化を行うための方法として、まずは現在の作業内容の見直しを行い、課題を発見することが必須です。その後、平準化・標準化を行うにはどうしたら良いかを検討していきます。作業の課題と平準化・標準化とのギャップが見えてきたら、費用対効果を検討しながら、自動化・自働化を推進していきます。
- 作業の見直し・課題の発見
- 作業の平準化・標準化
- 作業の自動化・自働化(スマートファクトリー / スマート工場)
それぞれの方法について具体的に見ていきましょう。
作業の見直し・課題の発見
省人化を行うためには、作業を見直し、課題を発見するという方法があります。比較的手軽にできる方法なので、まずはここから始めることを推奨します。作業内容の棚卸ともいえる見直しを行うと、現在では必要のない、単に習慣化された工程の存在に気付くことがあります。
何年もマニュアルが更新されていないことや、情報の共有不足によって無駄な作業が発生していることもあるでしょう。まずは前提として、業務効率化には業務プロセスの「見える化」が必要です。可視化された情報をもとに、どう改善するべきかを客観的な視点で検討し、実現に向けた新たな業務フローを確立していきます。
作業の平準化・標準化
作業内容を改善していく過程において、作業の平準化・標準化を行うことが、省人化につながります。工場における平準化とは、受注量と生産設備の稼働状況などを分析、そして作業量や設備稼働を平均化し無駄のない生産を実現することをいいます。あわせて、技術力のあるベテラン作業員が判断して行っている属人的な作業を見直したのち、手順や方法をルール化し標準化を図ることも有効です。誰もが、どの工程にも携わることができるようになれば、作業効率が向上します。
作業の自動化・自働化(スマートファクトリー / スマート工場)
省人化を行うために近年注目されているのが、スマートファクトリーといわれる取り組みです。スマートファクトリーとは作業の自動化・自働化を図るためのAIやIoTなどの技術を活用し、総合的に効率よく稼働する工場を目指すことをいいます。単に人の代わりにロボットを稼働させるという視点ではなく、さまざまなデジタル技術を用いて設計、生産、保守に対する総合的にデータ分析などを行い、現場業務に反映させます。昨今では工場全体の最適化はもちろん、企業全体としての取り組みとしても普及しています。
4. 工場の省人化の成功事例
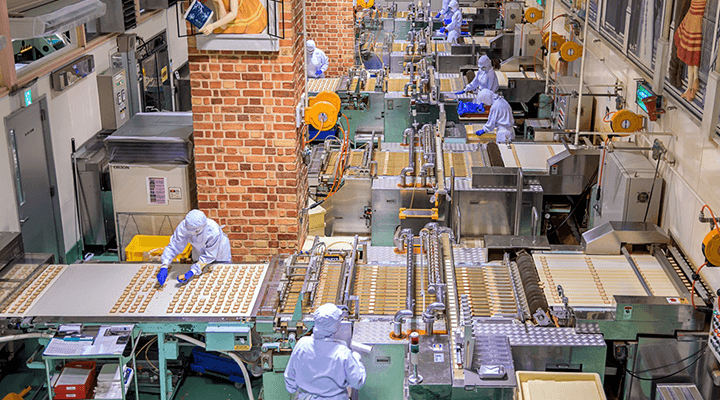
- 食品工場での成功事例
食品工場での省人化成功事例として、5名で1日8時間もの目視での色彩検査を行っていたのを、色彩選別機の導入により検査工程を2名で5時間程度の工程に実現し、省人化に成功しています。
- 大手メーカーでの成功事例
大手メーカーでの省人化の取り組みとして、ネットワークカメラとセンサーを使い、作業者や設備の稼働データを収集して生産工程を可視化しました。それらをAIによる分析で、生産ロスの改善が見込めるとしています。
当たり前に行っているプロセスの一部を自働化したことで、大きな省人化につながる事例は他にも数多くあります。事前に調査や分析により業務全体を「見える化」することで、取り組むべき課題が見えてくるでしょう。課題が見えたら省人化に取り組むことで初期投資は必要でも、長期的な観点でみれば大幅なコスト削減も見込める可能性も大いにあります。
5. 工場の省人化に「NetSupport Manager」の導入を!
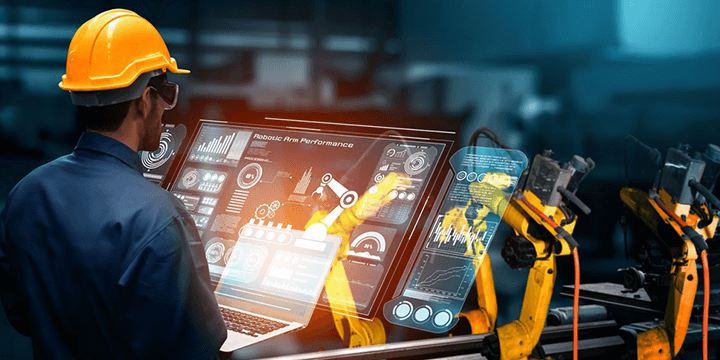
作業効率の向上だけではなく、品質や人手不足の問題を解消するための省人化の必要性が喧伝され、多くの企業で作業の自動化・自働化(スマートファクトリー)が進んでおりますが、一方では下記のような課題も生まれてきています。
- FAの制御機器の台数増
- 現場で、FAの制御機器に当日、週の生産計画を入力
- FAの制御機器に不具合でれば、現場で対応する
- FAの制御機器の全台を一括管理したい
スマートファクトリーを実現させたことにより人員削減が叶ったとしても、設備やシステム管理に多数の人員が必要になっては効果が半減してしまいます。
そこでおすすめしたいのが、 複数端末の俯瞰が可能なサムネイルビューを搭載したリモートコントロールツール「NetSupport Manager」です。
「NetSupport Manager」のデプロイ機能では、以下のことが可能です。
- リモートで複数のコンピュータにNetSupportパッケージを一斉インストール
- 選択したクライアント
- 特定のクライアント設定ファイルを作成し複数のコンピュータにダウンロード
- リモートで複数のコンピュータでNetSupportライセンス情報を更新
- リモートで複数のコンピュータからNetSupportパッケージを一斉アンインストール
主用途:FAサーバ / FA端末の、起動およびシャットダウン
その他:FAサーバ / FA端末の、遠隔操作、障害対応
また、この「NetSupport Manager」は、遠隔地にある工場の稼働状況をリアルタイムで確認したり、トラブル発生時のアラートを受けたりなど、いつどこからでも操作や管理が可能となれば、一元管理が実現できます。とくに拠点が多い製造業などでは、定期メンテナンスやトラブル対応に要していた人員コストも削減でき、かつ対応時間も大幅に短縮することができます。
大規模工場での事例では、広大な敷地内で点在するサーバや、端末の起動およびシャットダウンのための移動に時間がかかり、必然的に障害発生時の迅速な対応もできない状況が、NetSupport Managerの導入により改善されています。
さらに、同梱されているゲートウェイ機能により、自宅などどこからでもセキュアにリモート接続環境を構築できます。それゆえに、サードパーティー製クラウドサーバを経由する必要がなく、セキュリティ面でも安心です。工場の省人化ツールとして、NetSupport Managerを検討してみてはいかがでしょうか。
6. まとめ
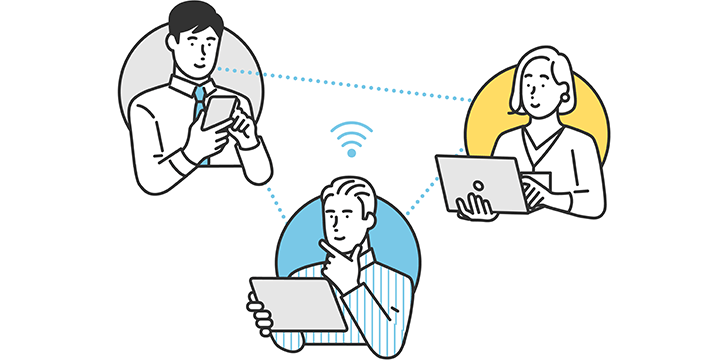
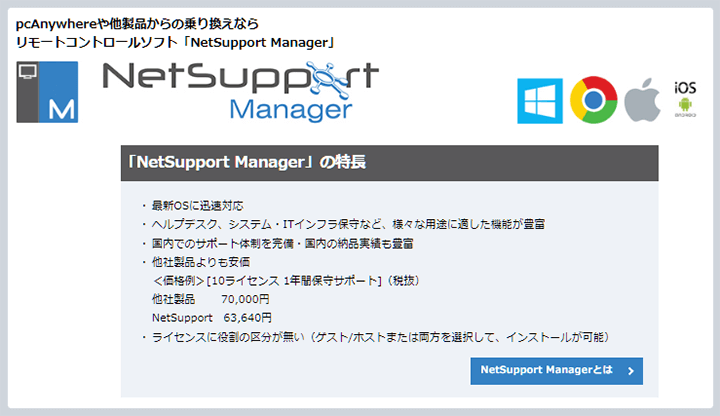
工場の省人化は、どの企業でも取り組むべき課題として認識しているのではないでしょうか。そのための手法はいくつかありますが、デジタル技術を活用し工場での生産現場の状況を可視化することは、どの業種においても重要なポイントとなるでしょう。自社組織に最適な省人化の仕組みを構築される際には、NetSupport Managerの導入をぜひご検討ください。
30日間の無料体験版を用意していますので、ぜひお気軽にご利用・お問い合わせください。